Honoring the most outstanding critical thinking experts in the world
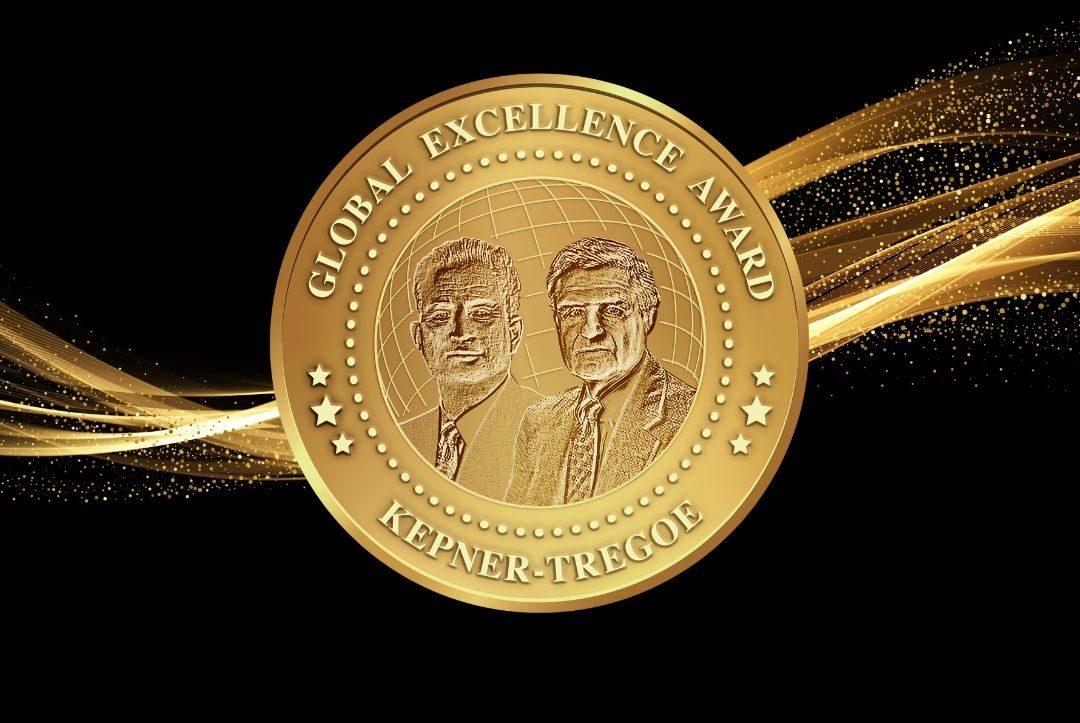
Benjamin Tregoe and Charles Kepner were the pioneers of rational process development. The KT Excellence awards are bestowed on individuals, teams, and organizations that distinguish themselves as being the best in the world in the application of critical thinking skills to improve the performance of business systems.
Legacy
For over 30 years KT has been honoring the most outstanding experts in the world with an award program formerly known as the Process Achievement Awards, that has grown in prestige each year since 1994.
Evolution
Since 2022, KT has expanded its awards program and renamed it the Kepner-Tregoe Global Excellence Awards. There are a total of 12 awards divided into three categories. See below for more details.
Kepner-Tregoe Excellence Awards 2025
Kepner-Tregoe Excellence Awards 2024
Kepner-Tregoe Excellence Awards 2023
Kepner-Tregoe Excellence Awards 2022
Individual Awards
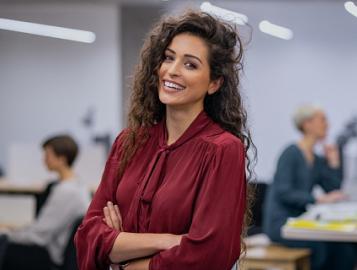
Bestowed on individuals who have demonstrated exceptional skills and abilities as well as succeeded in outstanding application of KT technology in their relevant area of expertise.
Awards under this category:
- Program Leader of the Year
- Facilitator of the Year
- Coach of the Year
- Rational Management Executive of the Year
Team Awards
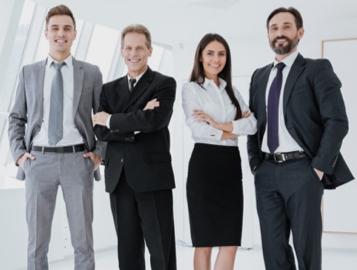
Bestowed on teams who have demonstrated global benchmark excellence in using KT methodologies in the resolution of complex issues.
Awards under this category:
- Problem Solving Excellence
- Decision Making Excellence
- Situation Appraisal Excellence
- Combined KT Technologies Excellence
Organization Awards
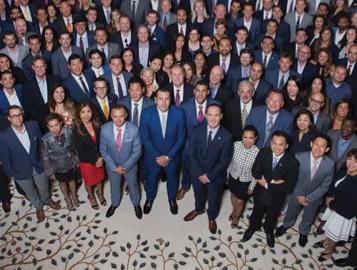
For the implementation and integration of the KT methodology within a particular function, facility, division, region, or company.
Awards under this category:
- Excellence in the Utilization of KT Process in Manufacturing Operations
- Excellence in the Utilization of KT Process in Service Operations
- Human Resource Capability Development Program Excellence
- Critical Thinking Cultural Excellence Award
Get in touch to find out how you can take part!
Any Questions?
Feel free to contact us for any details or information